Aqua-Puss MK1 AP2 (1998) Style PCB Now Available
- Ryan
- Feb 15, 2021
- 4 min read
Updated: Jul 11, 2022
Diving into a bit into my research into the Aqua-Puss MK1 AP2 as well as re-creating the circuit in a way that pays tribute to the original, however, offers a drop-in retrofit into an MK2 enclosure. Another fun announcement is that I'm opening an e-commerce outlet directly on this site and will be adding more DIY items as well as full builds as they become available. Check it out: Here

Recreating the original Aqua Puss really is the first pedal that has ever sent me down the rabbit hole. From my internet research, a proper clone of one does not exist, and minimal DIY resources are available. There is a pretty epic thread of a team of folks in https://www.freestompboxes.org/viewtopic.php?f=7&t=4216 reverse engineering an AP2 unit. This thread kicked off Mad Bean's Aquaboy PCB which started off as a tribute to the Aqua Puss, however since the Aqua Puss is largely a Boss DM-2, Madbean reverted the goal of the board to be a DM-2 circuit clone versus the Aqua Puss. Technically, you could modify the AquaBoy to build an Aqua Puss and I've done this a few times with great results. It still felt funny and I wanted to go a little deeper than that to make it look like a real AP2 so I retrofitted a board into my MK2. I retrofitted one more time using a Suchahardman PCB with very favorable results. Even with these favorable results, I wanted something that was built specifically for the MK2 enclosure and since I have the PCB design making skills, I thought I would revisit that.
Quickly let me recap the reason why I want to recreate an Aqua Puss so bad...
John Mayer (surprise surprise!) used the MK1 AP2 from the beginning of his career until ~2013 Born & Raised Tour where he switched over to an MK1 AP1. John Mayer Trio, Where the Light is, Continuum, etc. had the AP2 present.
They are out of production. FORBIDDEN FRUIT!
Expensive and I can't afford the ones that pop up online for $2,000+ USD.
Some pictures of John's Aqua Puss MK1 AP2. You'll notice one has LOMARK on it which I have no idea what it means. Maybe a repaired unit? The AP1 is different than the AP2 which I'll get to in a later entry.
Curiously, the FreeStompBox forum research had a few things that didn't make sense to me. The unit they used (I don't have a picture) must have been an extremely early prototype AP2. Every single picture of the AP2 I have seen is mostly comprised of carbon film resistors which are not the EIA E96 resistor decade compatible. They also did not document what capacitor type was used in each position. If I wanted to be sure I was making the best clone as I could, these things would matter, or at least they do on paper. The challenging bit was finding the 24mm PCB Alpha pots. As a potential alternative to 24mm pots, I also designed 24mm/16mm up-down-converter isolation PCBs so sourcing of pots will not be a gating factor in this build. Using EasyEDA.com to do the design and triple checking each measurement, my PCB design seemed to be ready for production!
After scouring through Mouser.com to find all the parts and sizes that match the original AP2, I was ready to build. I don't have many pictures of the build in progress due to time constraints however I am really happy with the end result! I picked up some soft switches from Love My Switches for the feel of the original's 3PDT. I also had to use Lumberg stereo jacks for clearance reasons. The internal trim pots have been modified to use multi-turn mechanics. This allows fine adjustment of clock frequency, bias, and "cancel" calibrations.
The PCB is for sale at my online shop here
DIY Resources
Bill of Materials and component identification.
https://docs.google.com/spreadsheets/d/1ij8Q3dKeb858STPtWmEE4nQqr_ChNIKrd6uZgG44oaY/edit?usp=sharing
1:1 PDF for drilling, etc.
Calibration
Calibration can be done without using an oscilloscope. It is recommended that you have a digital multimeter with a clock cycle frequency counter like the Proster VC99. The trim pots are 25 turn multi-turn so "middle" will be rotating them all the way to one direction until you hear the limiter click, and then counting 12.5 turns. I like Madbean's explanation of the calibration procedure (adapted for my PCB).
Make the following adjustments before beginning:
Mix control at the center.
Delay at the max position.
Feedback at about 1/3 up.
BIAS and Cancel trim pots to their center position.
If you have frequency measurement on your DMM, adjust the Clock trimmer to about 6.5kHz while probing the TP_CLOCK test point. If you don’t have this feature on your DMM, set the Clock trim half-way up (note: this is when using a 9v supply). Audio probe TP_BIAS while either strumming the guitar or send some audio through the input of the circuit. Adjust the BIAS trimmer until you get delay passing. The range over which the trimmer will result in the delay is usually about 1/4 to 1/6 of its entire rotation. Continue refining the position of BIAS until you get the smallest amount of distortion on the delay signal. Now probe TP_CANCEL to confirm it is also passing delay. If it does not, make sure that you have clock frequency on both pins 2 and 6 of the MN3005. Now finely adjust the CLOCK trimmer until just before you hear any high pitch whine in the audio path. This is the maximum delay setting. The clock frequency should land somewhere between 6 and 7 kHz. Unless you are using an oscilloscope to calibrate the delay, leave the Cancel trim in the center position. When I tested a AP1, the max clock frequency measured 6.2kHz @ 9.21VDC supply voltage.
If you're using an oscilloscope, the BOSS DM-2 instructions work well for this. I had a hard time getting the two waves to trigger on my oscilloscope so I tried a few times to get something that resembled two waveforms adjusting and coming together.
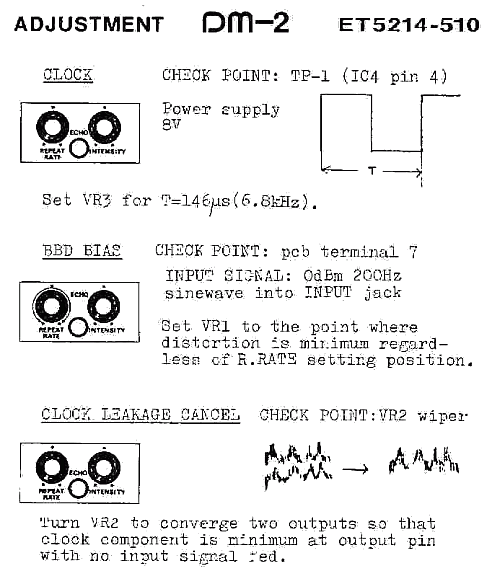
Getting ready to dive in on one of these. Will likely have to build my own enclosure unless you know someone with a dead soldier to donate to the cause! :D